The Grantham Southern Relief Road Project is a new bypass with the purpose of linking the A1 and the A52 to the south of Grantham. Phase 1 and 2 involved construction of the motorway junction on the A1, including connecting roads and roundabouts. Phase 3 involved the construction of a new two lane multi span bridge over the combined East Coast Main Line, and the River Witham.
The scheme was delivered by Galliford Try acting as Main Contractor on behalf of Lincolnshire County Council and Lincolnshire Highways, in partnership with Designers WSP.
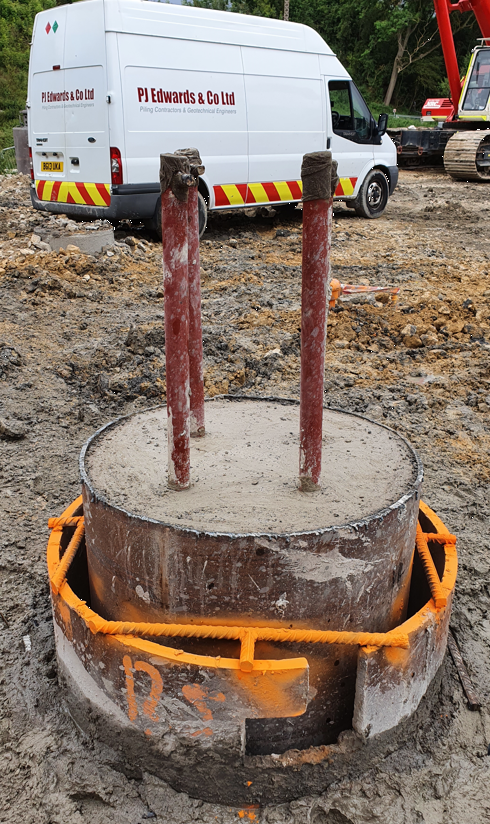
PJE were appointed to install the piled foundations for the main bridge required for Phase 3 of the scheme. Piling works on this project consisted of 2 sections; the first section incorporating the installation of 48no 900dia Rotary bored piles to depths of 36.0+m BGL on 4 individual piers. This section also included the construction of a preliminary test pile to confirm the bearing capacity of the founding bedrock.
The second section of piling work involved installation of a further 109no 900dia Rotary bored piles to depths of 35+mBGL which were distributed over two piers and one abutment, with associated wing walls.
Prior to installation of any permanent working piles, PJE were instructed to install a preliminary test pile. In order to gain a true reflection of the underlying rock capacity, a double lined test pile was installed to negate any skin friction contribution above the rock. PJE began by installing a 8.0m section of 1300dia segmental casing into which was pitched a 16m outer 1016mm diameter slip casing. A third smaller diameter inner casing was then installed in order to debond all ground above the mudstone socket. A cage was then inserted and the pile concreted using tremie techniques
The results of this preliminary test piling were then used by WSP to finalise the pile design for the main structure.
Once the final design was complete, PJE remobilised and began installation of the main works piles for Piers 1 to 4. For this section PJE benefited from the newest addition to the drilling fleet by using a 130t Mait HR420-800 rotary rig. The advantage of this rig was to allow installation of very long strings of temporary casing and negate the need for the use of support fluid.
Pier 3, which was positioned between the ECML and the River Witham, had to be accessed via a temporary bailey bridge. Due to space and weight limitations, PJE brought in a smaller 85t Mait HR260 drilling rig to install these piles. This pier was also serviced by a telescopic crawler crane, a Liebherr LTR1060, to further assist with working room constraints and weight limits on the bailey bridge.
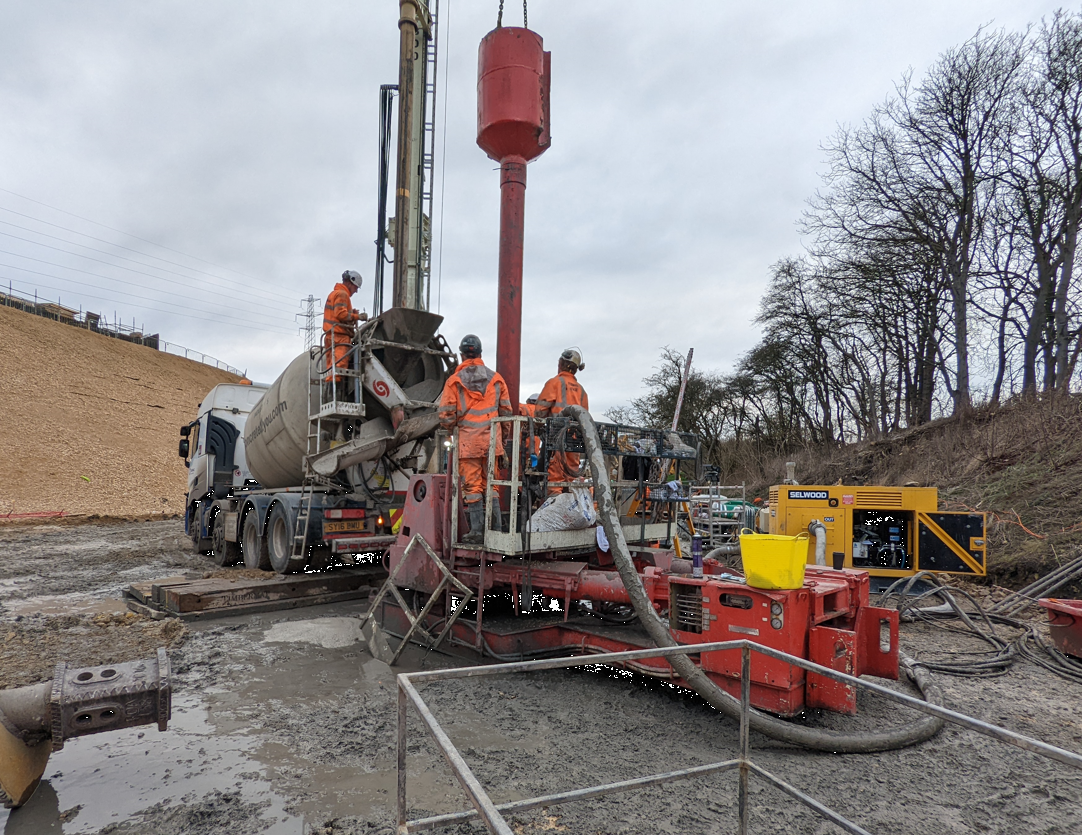
During the completion of the first section of piling works, PJE assisted the project team by providing buildability advice for the next section of work where potential embankment movement, and deep ground fissures had been identified by further site investigation on the eastern approach to the new bridge.
PJE worked with both Galliford Try and WSP to mitigate the risk to pile integrity as a result of ground fissures, and assisted in arriving at the most cost effective approach for options to stabilise the embankment for the new bridge construction. The result of this process was to extend the original bridge spans by a further 2 piers and one abutment on the eastern side, all supported on deep piled foundations.
PJE began installation of the second section of piles by carrying out concreted trial bores in order to gauge the potential impact of inground fissures within the underlying limestone strata. Following successful installation of these trial bores, work began on the permanent piles working on dedicated terraced platforms for each support which included detailed discussion with network rail due to the close proximity of some work to the adjacent East Coast Main Line.

Although no further load testing was carried out on the scheme, all piles were integrity tested using thermal image profiling which provided a very buildable alternative to traditional sonic logging, and had the advantage of providing very quick feedback on the as built integrity of each pile.